Moore’s Law for EVs? Better Ask Koomey
- Deaglán Ó Meachair
- Jan 23, 2022
- 6 min read
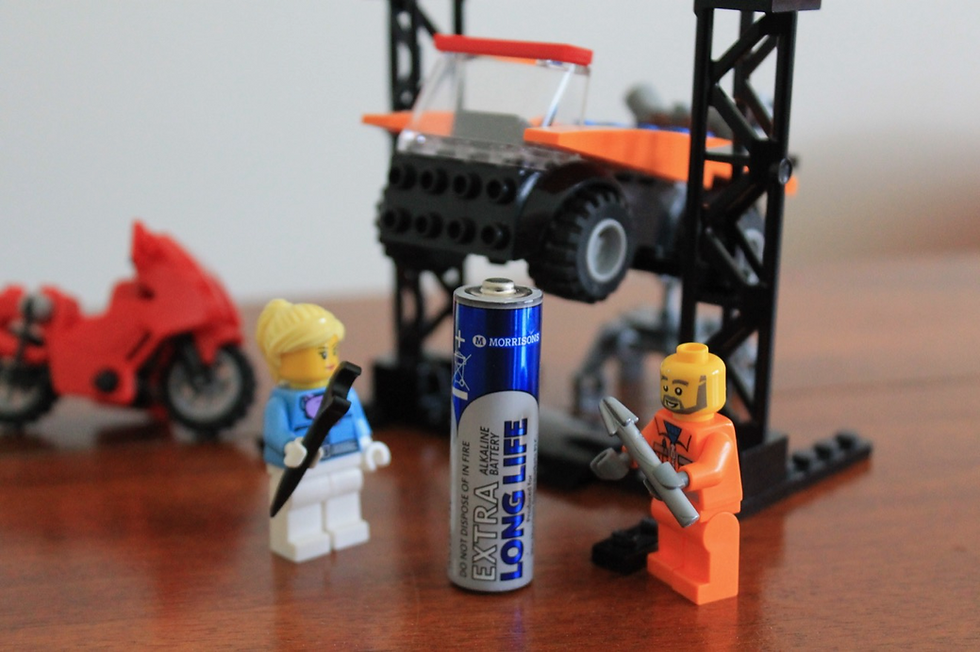
In considering how electric vehicles will improve over the coming decades, it’s useful to consider history. Specifically, it’s worth considering the history of consumer electronics, and how mobile devices have dealt with power consumption and battery life. We will examine how the computer industry has dealt with power-hungry devices, developed solutions to suit, and look at what might read across into electrified transport.
Moore’s Law and the rise of the mobile device
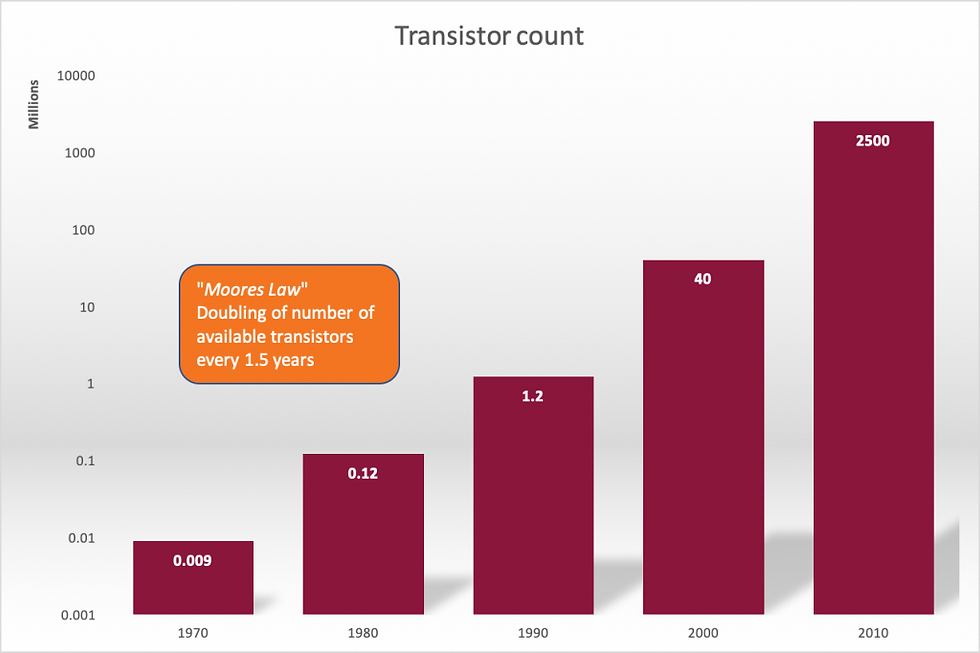
Most people have probably heard of Moore’s Law in relation to microprocessors – the doubling every year of the number of components on an integrated circuit. This trend has largely held true over 5 decades, and shown that ever greater processing power can be squeezed out of the same CPU real estate – effectively allowing for exponential growth in computing power. There is some evidence to suggest that the progression may be slowing in recent years, but time will tell (!)
Not quite as well known, but no less influential, is Koomey’s Law. This describes that the number of computations achievable per unit of energy dissipated would double every 18 months. While intrinsically intertwined with Moore’s Law, this is a key trend in making computers mobile, as every decade, the amount of (battery) power needed for a fixed computing load will fall by a factor of 100.
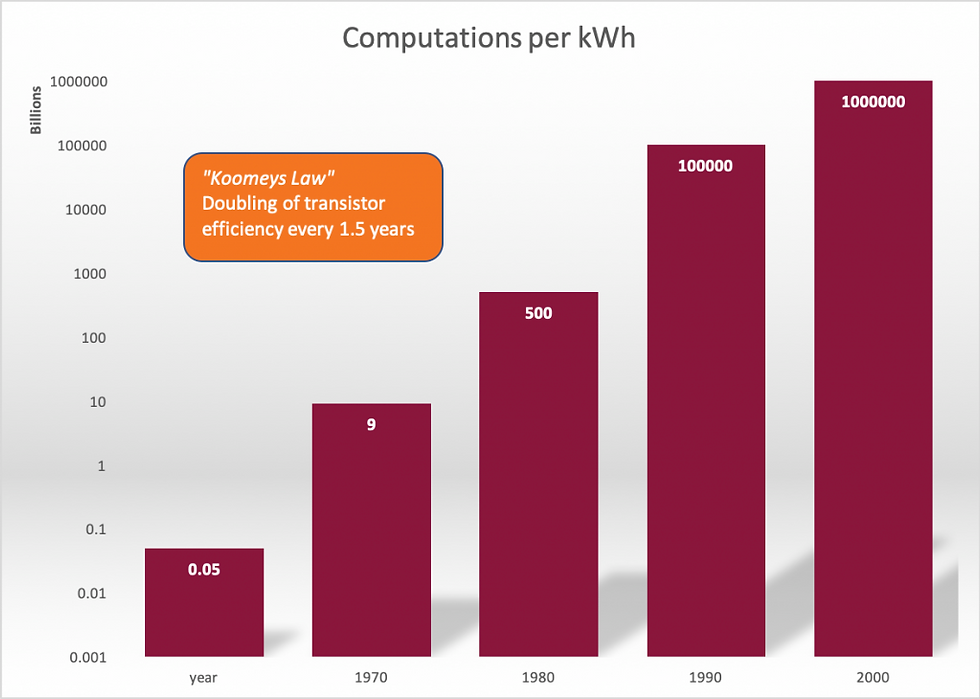
While computer cost and power efficiency has been growing exponentially for decades, the same isn’t necessarily true for batteries. When mobile computers first gained popularity, the cost and power density of batteries quickly improved.
However, in contrast to the development of the processors, the battery performance improved at a relatively slow pace – doubling every decade. In the same decade, the power efficiency of the CPU had increased 100-fold.
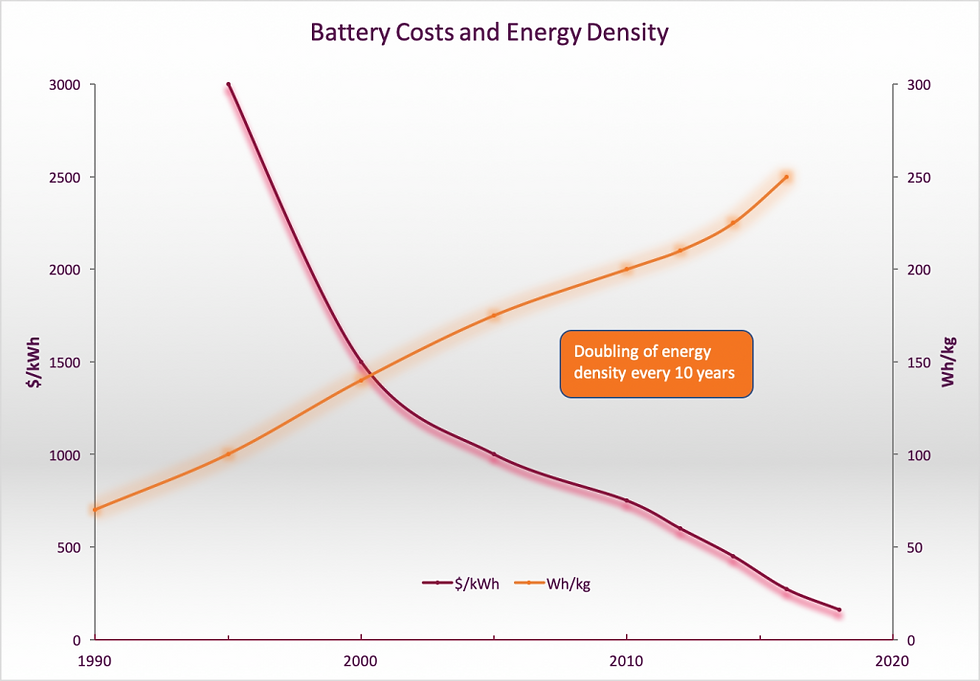
So, if we now consider battery-powered vehicles, it should be clear that while batteries will improve in terms of available power per unit mass (or volume, or cost), this alone won’t solve the restrictions of vehicle range. While it is probably true that EVs bring vast economies of scale to bear on battery research, the R&D firepower (and budgets) of the consumer electronics industry shouldn’t be discounted. It’s anyones guess if vehicle engineers will bring any significant battery breakthrough that has thus far eluded us.
Efficiency matters more than battery chemistry
Energy is required to move something, regardless of how that movement occurs. Put more scientifically, energy conversions take place to enable movement – a pebble falling from a cliff converts potential energy to kinetic energy, a dog chasing a car converts chemical energy (food) into kinetic energy, while the car being chased by the dog converts either chemical energy (oil) or electrical energy (battery charge) into kinetic energy. Energy efficiency can be thought of in terms of how successful a process is in turning stored energy into useful energy.
So far, so unsurprising.
So let’s look in a bit more detail at how energy efficiency works for moving a cyclist. Depending on the bicycle, our cyclist needs between 5Wh and 15Wh of energy to travel one kilometre. As most people are familiar with riding a bike, it is useful to consider what an efficient bike might look like, compared to an inefficient one, and what “technical devices” make a difference (seen as most things relevant for a bike are relevant for other vehicles).
What would a cyclist do?
For most people an efficient bike would probably be an aerodynamic racing bike, with stiff narrow tires, low aerodynamic drag, and probably a well-oiled gear set. It should seem obvious, but most of the technical areas important to cycling are important to electric vehicles.
If you have ever cycled into a headwind, even at relatively low speeds, you will know why aerodynamics are important. If you’ve ever cycled up a hill, you’ll know why gearing, and by extension efficiency, is important. If you’ve ever experimented with different tires on the same frame, or even run a bike with under-inflated tires, you’ll know why rolling resistance is important.
An electric car will need between 120Wh and 200Wh per kilometre. Just like with the bicycle above, this consumption depends on solving largely the same problems. a quick comparison of electric vehicles in terms of aerodynamic efficiency shows that the ones playing close attention to drag coefficients are the ones getting the better efficiency scores.
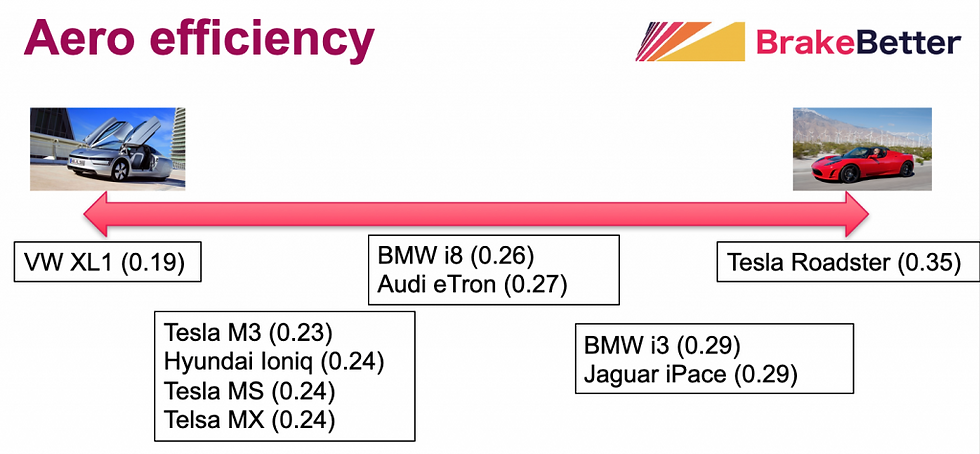
With a keen aerodynamic target at the design stage, it’s possible to make significant inroads. However, aerodynamic efficiency should be considered throughout the design process, and any surface exposed to airflow is an opportunity to eke out better results. Whether it’s active apertures, vortex management devices, dynamic ride-height changes or rethinking rearward visibility, beneficial effects can be found at any stage during the design of a vehicle.
So where else can energy efficiency be found? Well, if we consider where is the energy used, we can start to understand what we can do to improve efficiency. Thinking about our bike, as well as aerodynamic resistance, we can consider rolling resistance (our under-inflated tires and grime-filled wheel bearings, as well as brakes rubbing a wheel), internal powertrain resistances (poorly lubricated chains and cogs).
What can a vehicle (engineer) do?
While all these areas can directly translate into other vehicles, for electric vehicles, a number of unique optimization possibilities exist. If we consider the electric drivetrain, as well as reducing mechanical resistance, making better use of the available electrical energy is beneficial. This can be achieved in the design of the motor itself, the inverter and power electronics, as well as control models used.
Another significant area for EV efficiency is brake energy recovery. When applied properly, today’s initial efforts in regenerative braking can deliver up to 30% more driving range, but requiring only minimal extra components. The compelling part of the story is that as parasitic losses (such as rolling or aerodynamic resistance) are minimized, the regenerative braking dividend increases. It is also fair to say that brake energy recovery has some way to go in terms of returned range – today’s state of the art is a mix of new and existing solutions, to create a new effect. Once efficiency becomes ingrained as a core design aim in braking systems, those systems will become lighter, will drag less, will be more error tolerant, and crucially, return more energy.
Comparing and contrasting
When considering how to squeeze the most range out of an electric vehicle, it can be useful to compare the relative contributions of varying technologies. Below is an estimate of how much bang-per-buck it is possible to expect from some of the topics covered above. While it shouldn’t surprise anyone that battery capacity dominates any conversation on electrification, it is also true that battery costs dominate the commercial proposition of any electrified vehicle project. Reaching for more battery cells is not usually the best way to get more range, and more often than not, it simply isn’t physically possible to shoe-horn more cells into a pack. On the other hand, chasing down efficiency gains will unlock more range, extra power and material savings, and can often provide synergistic benefits in other areas.

A further commercial consideration for efficient technologies in vehicles is longevity or durability of the battery. Simply put, if the battery has to cycle through less energy, it will last longer. Therefore, if the vehicle systems contributing to range are to protect the battery from excessive loads, they too must have long term horizons in terms of their functionality. If the battery warranty is the longest warranty on the vehicle then the performance of all relevant parts contributing to energy efficiency need to be considered.
An emerging area of efficiency is that of demand management, or predictive efficiency. This approach means giving the driver more information to make better energy choices (such as less aggressive accelerations or earlier braking interventions). But it also means using spatial data to allow the vehicle to configure itself differently (such as lowering ride height at specific points on a route). Looking further forward, sharing of data between vehicles, so-called swarm data, can lead to much more powerful demand management – offering up the possibilities of vehicles learning from each other as to what configurations and actions can lead to the best energy outcomes.
So what have we learned?
Waiting for the next battery breakthrough is going to take a while.
But batteries aren’t the only show in town, and we don’t have to sit on our hands.
There are plenty of other areas with low hanging fruit, and plenty of areas for further development, some of which can overlap to make compelling technological advances. It’s possible to foresee a decade of battery improvements allied to efficiency improvements will get EV ranges into four figures.
Deaglán Ó Meachair has worked in chassis technology across VW Group and select global start-up OEMs for over two decades. He has engineered the fastest, heaviest, and most refined vehicles, meeting the demands of the most discerning drivers. Deaglán is a member of and an instructor in Brake Academy.
Comments